FENDER TYPES
A variety of factors influence the specification of a fender system; these include local marine environment, wind and wave exposure of harbour basins, size and type of vessels expected to berth against them, the speed and direction of vessel approach and the type of berthing structure.
There are many types of rubber fender used for various applications, most moulded rubber fenders are characterised by what the fender industry defines as “buckling column” type. They have a geometric shape that produces a non-linear force/deflection curve. The advantage of this is to develop a considerable amount of work (or energy), for a given force required to compress the fender. Compare this to say a steel spring with a linear force/deflection curve, the energy absorption of the buckling column type would between 40 to 70% higher for the same force and deflection. Although this makes them very efficient energy absorbing mechanisms, it does mean that they can generate very high levels of reaction force with light impacts.
Other performance characteristics of the fender will be dictated by its manufacturing process: Most manufacturers offer a variety of rubber hardnesses for their moulded fenders which increases the range of performances available. Compound formulation, the blending of rubber compounds such as natural rubber and synthetic SBR types, embedded steel surface preparation and bonding agents, and building of the fender itself and moulding technique are all critical in producing a dimensionally stable and repeatable product.
Rubber fenders are also subject to correction factors applied to their performance. A typical ± 10% variation in energy and reaction tolerance should be considered in their design. Ambient temperature can have a significant effect on the fender performance, as can the speed at which the ship impacts the fender and any rotation caused by the ship compressing the fender at an angle, All of these factors will be compounded to change its performance from the manufacturers catalogue ratings.
The service life of a fender depends on the mechanical and physical properties of the rubber compound. Thus usually, the higher the properties the longer the service life and the lower the properties (for example use of recycled rubber) the lower the service life. The design of the fender system and its facings, steel frontal panel and restraint chains are all critical to its longevity. A well designed and maintained fender should have an anticipated life span of 20 to 30 years.
Here is an overview of commonly used fenders:
MAIN COMPONENTS OF A TYPICAL FENDER SYSTEM
- Rubber fenders absorb the kinetic energy of the berthing vessel. The rubber units commonly in a fender system are cone, cell or element types, they are designed for varying impact speeds, temperatures, berthing and bow flare angles, and occasional or frequent use.
- Frontal panels transmit the impact forces from the ship to the rubber fender. They are designed to provide low hull pressures and withstand other conditions such as line loadings depending on specific anticipated berthing conditions. They are robust complex painted steel fabrications designed to resist combinations of bending, shear and local buckling. Generous chamfers should be provided along their tops and sides to prevent hulls from snagging.
- Low friction pads, the frontal panels are typically faced with ultra high molecular weight polyethylene (UHMW-PE), which provides a low friction hard wearing surface to the fender system
- Weight chains; support the combined weight of the frontal panel which can be heavy, as well as the vertical downward friction forces.
- Shear chains; resist the horizontal shear forces acting on the fender, this is particularly relevant where a vessel might range along the berth and slide across the fender whilst being compressed.
- Tension chains; are particularly important for preventing the rubber fender from being pulled in tension from a vessel making a low level impact on the frontal panel.
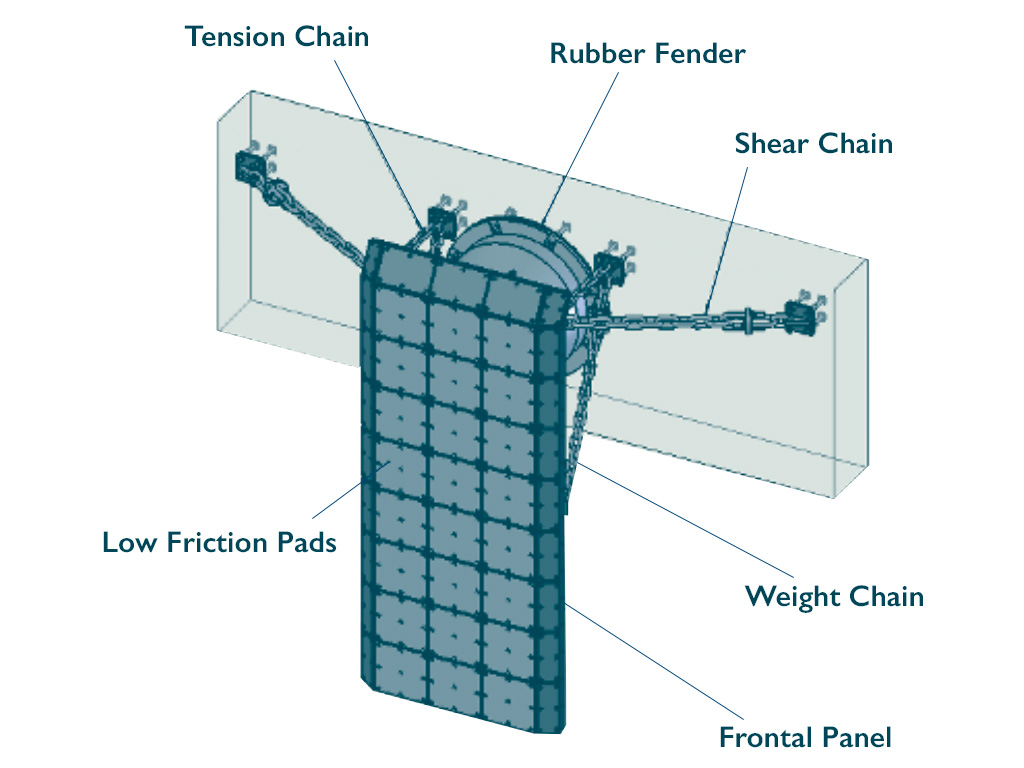